Wide application of coal rock method in the field of coking
The coal and rock analysis system has a wide range of applications in the field of coking with its unique characteristics. It can overcome some of the shortcomings of coal chemistry methods. For example, the coal quality method is used to evaluate the coal quality, and the coal coke coal blending is guided.
First, evaluate the quality of coal from coking enterprises.
1. The vitrinite reflectance is the best indicator for evaluating the degree of coal metamorphism.
Although there are many indicators for evaluating the degree of coal metamorphism, such as the commonly used volatile Vdaf, calorific value Qnet, carbon content Cdaf, etc., these coal chemical indicators are not a single coal rock component, and it is difficult to avoid interference from other components. For example, if a certain coal stable component content is high, because the stable component volatile content is high, Vdaf is used to evaluate the degree of metamorphism, and the degree of metamorphism may be lower than the actual. The morphological grade maximum reflectance index is used to judge the degree of metamorphism. Since the single component is measured and is not interfered by other components, the degree of metamorphism can be accurately judged. The range of coal reflectivity distribution of different grades of coal in China is as follows:
Coal species | lignite | Long flame coal | gas coal | 1/3 coking coal | Fat coal | Coking coal | Thin coking coal | lean coal | Lean coal | anthracite |
R0max % | <0.5 | 0.5-0.6 | 0.65-0.8 | 0.8-0.9 | 0.9-1.2 | 1.2-1.5 | 1.5-1.70 | 1.7-1.9 | 1.9-2.5 | >2.5 |
2. The coking property was evaluated.
In the coking coal of coking enterprises, the degree of metamorphism of coal is the same, as R0max is the same, but its coking properties can vary greatly. Such as:
Coal type | R0max | M40 | M10 | Fusible component |
Fengwu790 | 1.266 | 72.6 | 10.4 | 62.7 |
Carboniferous #Second mine | 1.256 | 66.2 | 10.7 | 53.3 |
This difference can be explained from the reflectance profile obtained from the reflectance measurement. Although R0max is the same, its reflectance profile is different. Some reflectance distribution histograms are concentrated in a narrow range, and some are distributed over a wide range. This is also seen from the difference in the standard variance S value.
The research shows that the vitrinite reflectance distribution map of coal has a large area surrounded by R0max = 1.1, and the better the coking property. This explains the phenomenon that R0max is the same and the coking property is different.
3. Determine the unity of coal.
In recent years, many coking enterprises have come to coal for coal blending. The mixed phenomenon of fat coal and coking coal with better coal quality is more serious. There is less mixing of gas and fertilizer. If mixed coal with 1/3 coking coal, a small amount of coking coal and lean coal, its Vdaf and G value can be similar to that of fat coal or coking coal, but it does not play the role of fat coal or coking coal in coal blending. The use of such mixed coal as fertilizer and coking coal will inevitably reduce the quality of the coke. The vitrinite reflectance profile of coal is the only way to identify single coal and coal blending. To this end, the state has established relevant standards: “Criteria for the determination of the reflectivity distribution of coal vitrinite groups”.
The reflectance profile of a single coal is a single peak with a standard deviation of less than 0.2. The blended coal is bimodal or multimodal with a standard deviation greater than 0.2. As shown. Judging whether the double or multi-peak is based on whether there is a "notch".
This national standard does not provide a detailed description of the depth of the notch, which is inconvenient for use. In the MSP 9000C coal and rock equipment, it is convenient to convert the 0.5.th order reflectance map into a 0.1th order reflectance map to remove the small “notch”. If the “notch” still exists, it is considered “concave”. mouth".
4. Determine the approximate proportion of coal blended.
For coal blending, the approximate coal blending ratio can be determined according to the area of each peak on the vitrinite reflectance map.
For peaks without overlapping portions, each peak represents a grade of coal. The mixing ratio can be determined in a simple way. In the MSP 9000C coal and rock equipment, the upper and lower limits of the reflectivity of each peak can be determined by the rolling rod provided by the software, and the peak area is determined by the integral to determine the mixing ratio.
For the overlap between the peaks, since there are two or more peak components in the overlap, it is not reasonable to determine the blend ratio by the method of determining the upper and lower limits of each peak.
The MSP 9000C coal-rock equipment provides a curve-peeling peak method for determining the proportion of coal blending. E.g:
5. Determine the content of the active inert component and its active inertia ratio.
Coal rock composition is one of the important factors affecting the properties of coal. The process properties of different micro-coal components are completely different.
The coal vitrinite of medium metamorphism has the best cohesiveness and coking property.
The shell group has a higher volatile content, such as the volatile content of the resin can be as high as 90%. Therefore, the contribution to coke formation is small, but due to its high hydrogen content, according to the mechanism of hydrogen transfer, the presence of the chitin group can improve the cohesiveness and coking property of the mirror mass group in coal.
The silk group is non-adhesive and needs to be bonded by other components during the coking process.
The vitrinite group and the stable group in coal are generally classified as active components, and the silk group is classified as an inert component.
The active components in the coal show a softening and melting phenomenon during the coking process, and the inert components have no softening and melting during the coking process.
Obviously, the proportion of each micro-coal rock component in coal is different, and its cohesiveness and coking property are inevitably different. E.g:
Chemical Process Properties of Coals in Huainan Coalfield
Ore layer | Analysis of micro-coal rock components,% | Industrial analysis | Tar yield |
Mirror group | Semi-mirror group | Silk group | Stable group | mineral | Mad | Ad | Vdaf | X | Y |
10 layers of coal | 58.4 | 9.9 | 15.4 | 15.6 | 0.7 | 2.2 | 7.6 | 35.84 | 45 | 10 | 10.32 |
13-layer coal | 46.3 | 7.7 | 19.4 | 25.9 | 0.7 | 1.98 | 8.0 | 42.64 | 65.5 | 10.5 | 15.51 |
Due to the same coal field, the upper and lower layers are not far apart, and the degree of metamorphism is basically the same. However, due to the high stability of the 13-layer coal, the Vdaf and tar yields are relatively high.
Japanese steel pipe company example: Japanese steel pipe company imports American coal and Australian coal, the same quality of single coal coke, but the US coal price is $88, Australian coal is $68, because of the high content of active coal in the United States and the high content of inert components in Australian coal. .
Therefore, the degree of metamorphism of coal and the micro-coal rock component are the two most important factors in the nature of coal. The vitroma group, which is also the active component, has a different degree of metamorphism and a large difference in properties.
6. Determine the wind oxidation of coal.
Coal with moderate to low metamorphism is susceptible to oxidation during storage. After the oxidation of coal, its properties change greatly, and the cohesiveness can completely disappear. It is difficult to play a corresponding role in coal blending. Therefore, coking enterprises should avoid the oxidation of coal.
When coal is slightly oxidized, general coal chemical indicators are difficult to reflect. The ignition point of coal is more sensitive to the oxidation of coal. However, the ignition point of coal is generally not measured in coking enterprises.
The method of coal lithology can quickly determine whether oxidation is possible before the coal properties change significantly, providing a basis for promptly using coal that is about to undergo significant changes in coal quality.
The method is to observe the vitrinite group in the coal. When the coal is slightly oxidized, irregular cracks will appear in the vitrinite group.
Attention should be paid to distinguishing the difference between such vitrinite oxidation cracks and endogenous fissures:
Osmotic group oxidation crack: no return.
Endogenous fissures in the vitrinite group: perpendicular to the coal seam.
When the oxidation is severe, a unique "oxidation ring" may also appear in the vitrinite group: the inside and outside colors of the circle are inconsistent.
7. Determine the reduction of coal.
The degree of metamorphism in coal, microscopic coal and rock components. In the case where the reflectance distribution maps are all the same, the coal quality may also differ, which is due to the difference in the reductibility.
Reducibility refers to the difference in the acid-alkaline pH value of the oxidation-reduction potential Eh of the water medium during the peatization stage of the coal formation process, which forms the influence of different environments on the coal quality.
In a water body with poor fluidity, the oxidation-reduction potential is low, and the coal hydrogen content generated in this environment is high, the tar yield is high, and the cohesiveness is strong. It is called strong reduction coal. The vitrinite group of strongly reduced coal will fluoresce under certain conditions. Fluorescence determination can be used to determine whether it is a strong reduction coal - this is also a coal lithology indicator.
Second, guide coal coke coal blending
1. The role of the reflectance distribution map of coal blending:
Using the measured single-mirror vitrinite reflectance distribution map and multiplying by the proportion of blending coal, the reflectivity distribution map of the blended coal can be synthesized.
On this coal blend reflectance distribution map, the actual percentage of different grades of coal is given according to the range of reflectivity distribution of different grades of coal. This is the only way to obtain the actual percentage of each grade of coal in the blended coal in the presence of blended coal.
In this way, it is possible to simulate coal blending on a computer, such as changing the coal type, changing the proportion of coal blending, and seeing whether the formed reflectance distribution map of coal blending is consistent with the reflectivity distribution map of coal blend with better coke quality. . If consistent or similar, the coal blending scheme is feasible.
Japan's coal blending experts believe that the R0max of coal blending is between 1.2 and 1.3, and the coke quality is better when the inert component content is 15-20%. The author believes that the R0e of coal blending is between 1.0 and 1.1, and S is between 0.3 and 0.35. The coke quality is good. The standard deviation is too small, indicating that there is a lack of coal in the coal blending. It is also possible to measure the reflectance distribution map of the blended coal, and find problems such as mismatching and mismatching in the coal blending process, and gradually changing the coal quality. Because the position of each peak in the blending reflectance map reflects its grade, the peak area reflects the percentage of its blending.
Third, the application in coal classification
As a second type of index for coal classification, the process properties of coal such as cohesiveness are used. There are many indicators for characterizing adhesion, such as Y, b, G, etc., each with advantages and disadvantages. A common disadvantage is that they can only comprehensively reflect the properties of the coal rock microscopic composition. When the microscopic composition of coal is very heterogeneous, coal with the same index of adhesion often appears, but reflects different coking properties. Some coals with similar process properties do not reside in the same grade. In particular, as described above, when the supplied coal is mixed coal, it is more difficult to determine the grade accurately. The reflectivity of coal and its microscopic composition reflect the nature of coal. They can accurately reflect the volatile matter and cohesiveness of coal, but not vice versa. In view of the above comments, countries around the world are gradually introducing coal and rock indicators into coal classification.
Whether the Soviet Union’s classification of industrial genesis as a unified classification of the whole Soviet Union began to be debated in 1970. Finally, the average maximum reflectance of the vitrinite group and the microscopic composition of the coal and rock were used as indicators in the coal classification.
The maximum reflectivity of the Mirror Group in the US ASTM standard is the coal classification index, and Bethlehem Steel has just adopted the active vitrinite reflectance.
Two indicators are generally used in Japan's coal classification, one of which is the maximum reflectivity of the vitrinite group and the other is the index of adhesion.
Others such as Poland, the Czech Republic, and France have adopted the vitrinite reflectance as a coal classification index, but the specific indicators for each country are inconsistent.
In 1970, the Xi'an Branch of the China Coal Research Institute proposed the industrial classification of the three indicators of the average maximum reflectance and the total amount of fusible components and the bond index G in the vitrinite group.
The International Coal and Rock Classification Conference has proposed a coal classification using a coding system, which was adopted in 1991 as an international coal seam classification. As a commercial coal classification scheme is still in the pipeline. The coding system first classifies coal into three categories according to the average random reflectance, that is, low coal rank coal (equivalent to lignite) with an average random reflectance of less than 0.6%, and medium coal rank coal equal to or greater than 0.6% ( Equivalent to bituminous coal) and high coal rank coal (equivalent to anthracite).
The "coal coal classification" is for medium and high coal rank coals with a total of 8 parameters and 14-bit code. The eight parameters are the morphological group random reflectivity, the vitrinite group random reflectance distribution characteristic map, the microscopic composition, the clamp pot expansion sequence number, the volatile matter, the ash, the total sulfur, and the high calorific value. The parameters of the encoding and the encoding of each parameter are listed in Table 2-7 to Table 2-14. For the coding of the morphological group random reflectance distribution characteristic map, please refer to Table 2-6.
Dividing the coal type according to the maximum reflectance average value Rmax of the vitrinite group
Coal type | Non-coking coal | gas coal | 1/3 coking coal | Fat coal | Coking coal | Thin coking coal | lean coal | Lean coal | anthracite |
Rmax | < 0.6 | 0.6-0.8 | 0.8-0.9 | 0.9-1.2 | 1.2-1.5 | 1.5-1.7 | 1.7-1.9 | 1.9-2.5 | >2.5 |
2. Coal and rock blending:
Coal blending technology is developed from conventional coal blending to coal blending.
2.1 The basic principle of coal and rock blending:
(1) Coal is a heterogeneous substance, and various micro-coal components of different process properties are mixed. They have different roles in coal blending. The softening and melting, as described above, during the coking process, the cohesive active component and the inert component which does not soften and melt without binding.
(2) The quality of the active components in coal is also different and varies greatly. Even the quality of the active components contained in the same coal is significantly different. For example, the vitrinite group has no cohesiveness when Rmax0<0.4 or R0max>1.7, and the adhesion is best when R0max is about 1.1.
(3) The inert component is an indispensable part of coal blending. In coal blending, the insufficient or excess content will lead to a decrease in coke quality.
(4) The coal bond occurs at the interface of the coal particles, and is bonded by the boundary reaction to form a crosslink bond. The liquid phase material produced by the coal heat medium diffuses along the interface. The quality of the interface is important for the quality of the coke.
(5) Coals with the same coal and rock index can be substituted for each other.
That is, the degree of metamorphism of coal, the composition of micro-coal rock, the map of reflectivity, and the degree of reduction of coal can be replaced by each other.
2.2 Coal and rock blending method:
(1), Ammosov-Shapiro Law:
A. Divide the coal and rock components into two categories:
Active component = vitrinite group + stable group + 1/3 semi-vitram group
Inert components = silk group (including semi-silk group) + 2/3 half vitrinite group + mineral group
B. Calculate the average mass of the active components, expressed by the SI index:
SI=(∑aIxI/∑xI)
i = 3~21
among them
aI - the intensity index of the active component containing a certain number of inert components with a reflectance of i/10, which can be obtained by looking up the corresponding figure. The graph is drawn from experimental data.
XI - the number of active components at a reflectance of i/10.
∑xI - the total amount of active ingredients.
C, calculate the composition balance index CBI
CBI=(100-∑XI)/∑Xi/bI
I=3~21
The molecular inert component content of the formula. ∑XI indicates the active group content;
bI is the best ratio of activity to inertia. At this point, the quality of coke is the best.
The CBI indicator reflects the proportion of the active inert group in the blending coal.
When CBI>1, it means that the inert component is too high, and when it is less than 1, it means that the content of the inert component is insufficient, and when it is equal to 1, it means appropriate.
Check the corresponding chart to predict the quality of the coke.
(2) Japan's official government drop law:
A. Calculate the coal blending R0max, and consider R0max to be the best when it is 1.2~1.3.
B. Calculate the content of the inert component, which is considered to be about 15%.
C. Consider the suitability of coal blending:
The Kelvin mobility index was used to investigate whether the softening and melting temperature ranges of each coal type overlap. If they do not overlap, add coal to overlap.
There is no Kiri's plastometer in addition to Baosteel in China, but it can be evaluated by investigating the interface bonding conditions of coke formation.
(3) Problems in coal and coal blending and their solutions:
The basic principle of coal and rock blending is reliable, but the relevant problems must be solved in the implementation.
In the Amosov method, it is necessary to determine the percentage of the active group in the 0.1th order range. This can be determined by the reflectance profile, which is provided by the MSP 9000C coal-rock equipment, but it is very difficult to determine the optimum ratio of activity to inertia for each stage. One method is to separate the various microscopic components by the method of separating the micro-coal components, and coke with different inerts to determine the quality of the active components. The workload is too large, and it is difficult to separate the coal rock components at a reflectance of 0.1 order.
A better solution is:
It is derived by measuring the capacity of the inertia.
Adding different proportions of standard anthracite coal to the coal sample and determining its bond index will give a curve of G value versus total inert matter content in coal (G-I curve). After many measurements, the G-I curves of different coal types are always straight. By extrapolating along the straight line to both ends, the G value when the total inert matter is zero can be obtained, which is denoted as GA, and GA is the pure active component mass. This method can also be used to determine the maximum capacity of various coals and the like. When a single coal or coal blend is added with different proportions of inert materials to refine the coke, and the microscopic strength MSI value is determined, there are:
MSI=f(R0max,A/2) is a parabola with a quadratic curve, so that the first derivative is 0, then the extremum, that is, the maximum value of MSI, is determined, and the corresponding A/2 is the best period. Live inertia ratio.
In recent years, inert components have not been found to be completely inert in many countries and in China. Some rich silky groups still have some activity during the coking process. Therefore, Amosov's method of dividing the active components is both hard and scientific.
A better solution is to divide the living inert component directly by the knot.
The method is: determining the content of the inert component in the coke, and then converting it into the content of the inert component based on the coal, thereby calculating the content of the active inert component and the ratio of the living inertia.
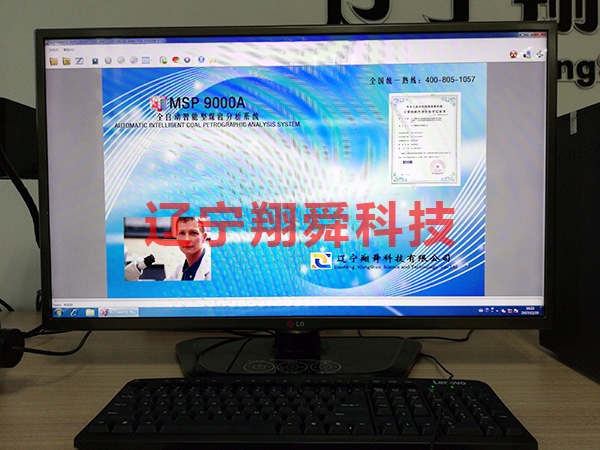